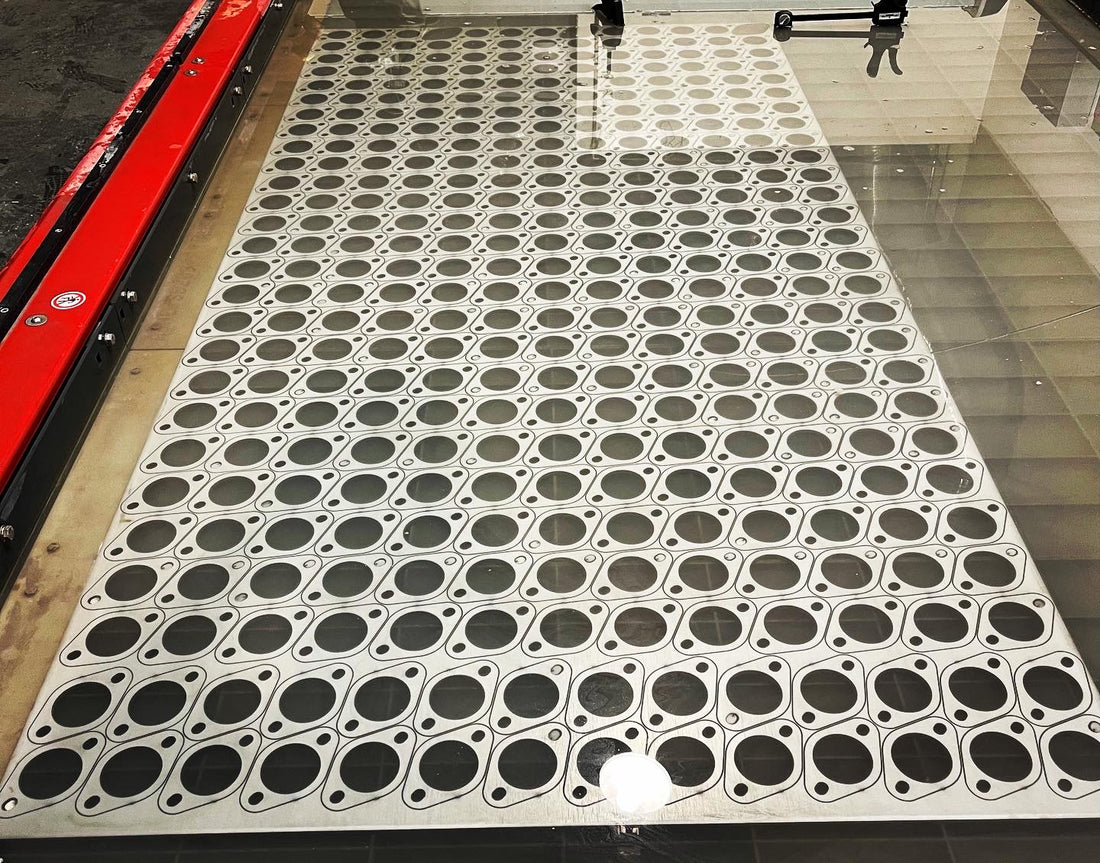
10 Benefits of Waterjet Machining
Waterjet machining is a cutting-edge technology that utilizes a high-pressure stream of water to cut through various materials. This process offers numerous advantages over traditional cutting methods, making it a popular choice in industries such as aerospace, automotive, and manufacturing. In this blog post, we will explore the top 10 benefits of waterjet machining.
1. Versatility
Waterjet machining is capable of cutting through a wide range of materials, including metals, plastics, composites, stone, glass, and ceramics. This versatility makes it a valuable tool for industries that work with diverse materials.
2. Precision
With waterjet machining, it is possible to achieve high levels of precision and accuracy. The stream of water can be controlled to cut intricate shapes and designs with tight tolerances, ensuring a superior finished product.
3. No Heat-Affected Zone
Unlike other cutting methods that generate heat, waterjet machining is a cold cutting process. This means that there is no heat-affected zone (HAZ) during the cutting process, minimizing the risk of material distortion or damage.
4. No Mechanical Stress
Waterjet machining does not subject the material to mechanical stress, as there is no contact between the cutting tool and the workpiece. This eliminates the risk of warping, deformation, or micro-cracking, particularly in delicate materials.
5. Environmentally Friendly
Waterjet machining is an environmentally friendly cutting method. It does not produce hazardous fumes, dust, or chips that can harm the operator or the environment. Additionally, the water used in the process can be recycled, reducing water consumption.
6. Cost-Effective
While the initial investment in waterjet machining equipment may be higher than traditional cutting tools, the long-term cost benefits are significant. Waterjet cutting eliminates the need for secondary finishing operations, reduces material waste, and increases productivity.
7. Fast Setup Time
Waterjet machining offers fast setup times compared to other cutting methods. The absence of complex tooling or fixturing allows for quick changeovers between different jobs, reducing downtime and increasing efficiency.
8. Minimal Material Waste
Waterjet machining is a highly efficient cutting process that minimizes material waste. The narrow kerf width and the ability to nest parts closely together optimize material utilization, resulting in cost savings and reduced environmental impact.
9. No Heat Distortion
Since waterjet machining is a cold cutting process, it does not cause heat distortion in the material being cut. This is particularly beneficial for heat-sensitive materials, such as plastics or composites, where maintaining dimensional stability is crucial.
10. Safety
Waterjet machining prioritizes operator safety. The absence of rotating blades or cutting tools reduces the risk of accidents or injuries. Additionally, the process can be automated, further minimizing human interaction and potential hazards.
In conclusion, waterjet machining offers a multitude of benefits that make it an attractive choice for various industries. Its versatility, precision, lack of heat-affected zone, and minimal material waste make it a cost-effective and environmentally friendly cutting method. With its ability to cut through a wide range of materials and its emphasis on safety, waterjet machining is revolutionizing the manufacturing world.